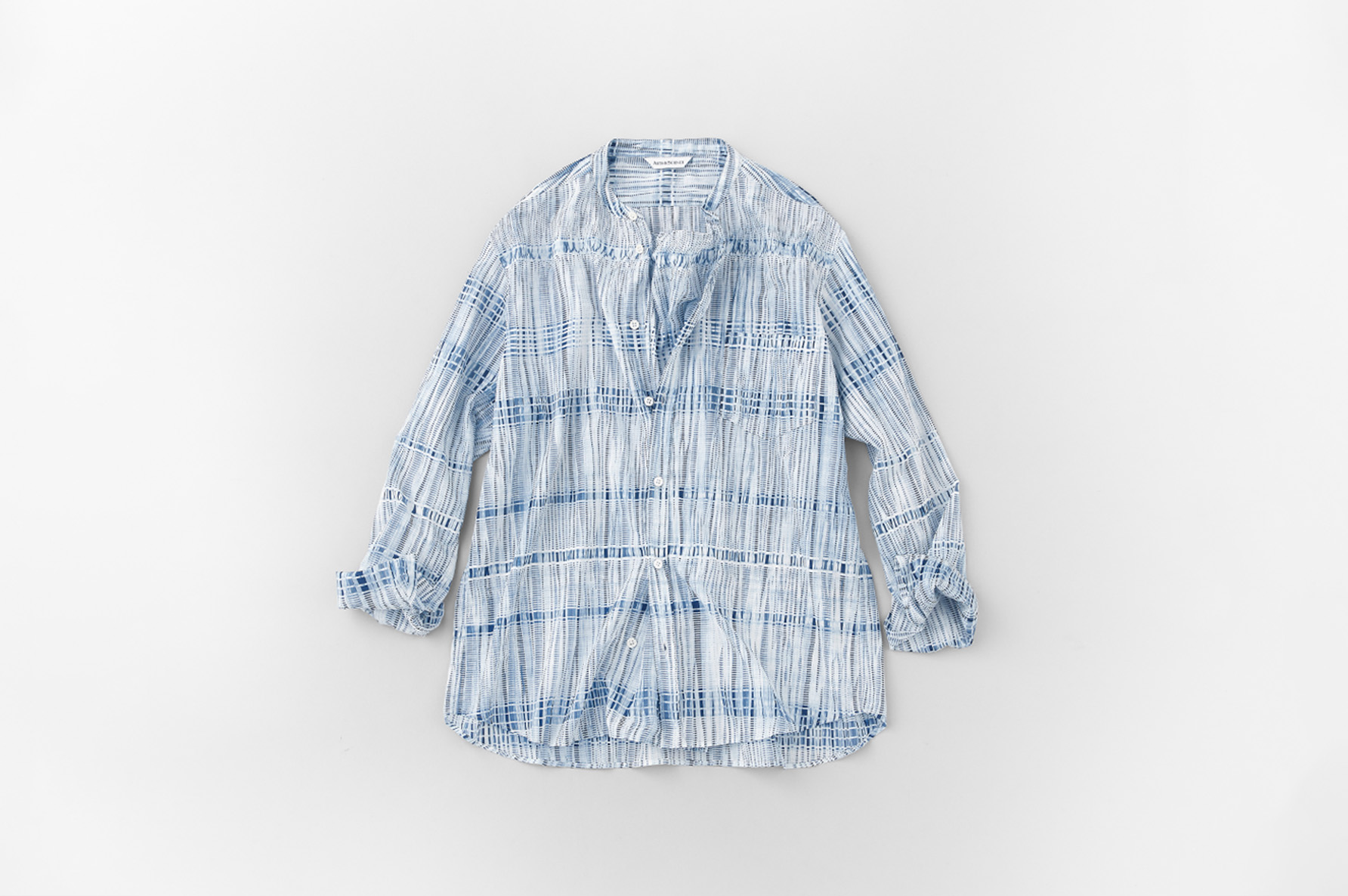
A&S 2024SS – ITAJIME Ai Check Lawn
In this series, we focus on the fabrics that are fundamental to the craftsmanship of ARTS&SCIENCE, introducing items made with these fabrics. For the 2024 Spring/Summer collection, we have primarily explored fabrics with distinctive production techniques, and for this season's final installment, we revisit the technique of Itajime dyeing, marking its return after several years.
ITAJIME Ai Check Lawn
ITAJIME AI CHECK LAWN is a fabric created through Itajime dyeing on 140-count ultra-thin cotton lawn material. Lawn, a lightweight plain weave fabric derived from linen or cotton, is a staple in A&S’s summer wardrobe, often used in blouses and dresses.
Itajime dyeing, a traditional technique dating back to the Nara period, involves tightly clamping fabric between boards to control dye penetration and create intricate patterns through pressure.
In A&S’s interpretation of Itajime dyeing, twenty boards with carved grooves serve as the basis for patterns. Fabric is sandwiched between these boards while being folded in, tightly clamped from both sides, and then immersed in an indigo dye solution to bring out the desired motifs.
This Itajime dyeing technique, developed through trial and error by an indigo dyeing workshop that inherited disused boards originally intended for Murayama Oshima Tsumugi, represents an original innovation. It involves two distinct stages, both entrusted entirely to the artisan’s tactile sensibility.
To perform Itajime dyeing, the first requirement is the preparation of the indigo dye solution. Indigo, believed to be one of humanity’s oldest dyes, is widely used worldwide, particularly in Japan, where it is mainly derived from the Japanese indigo plant of the Polygonaceae family.
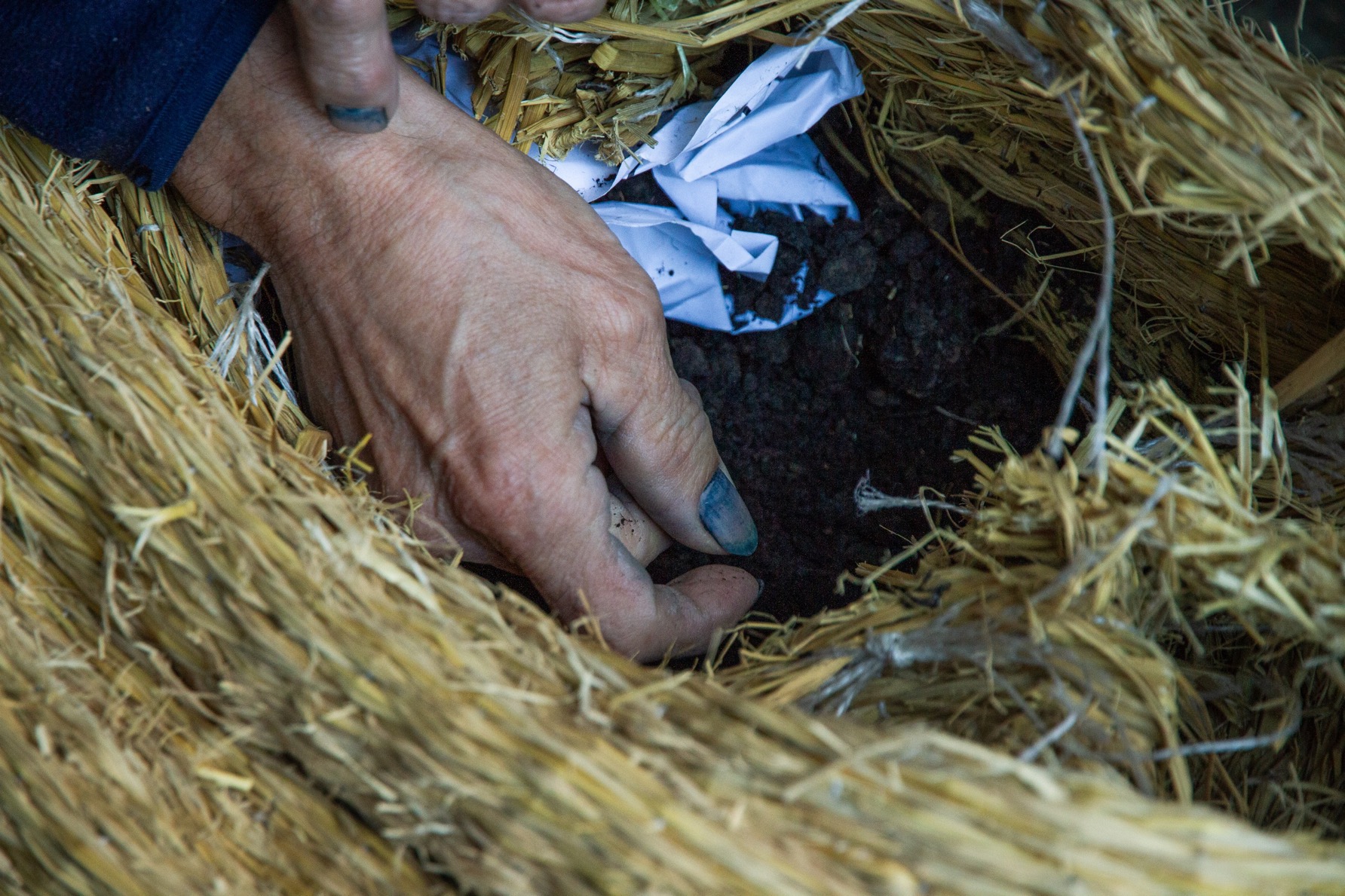
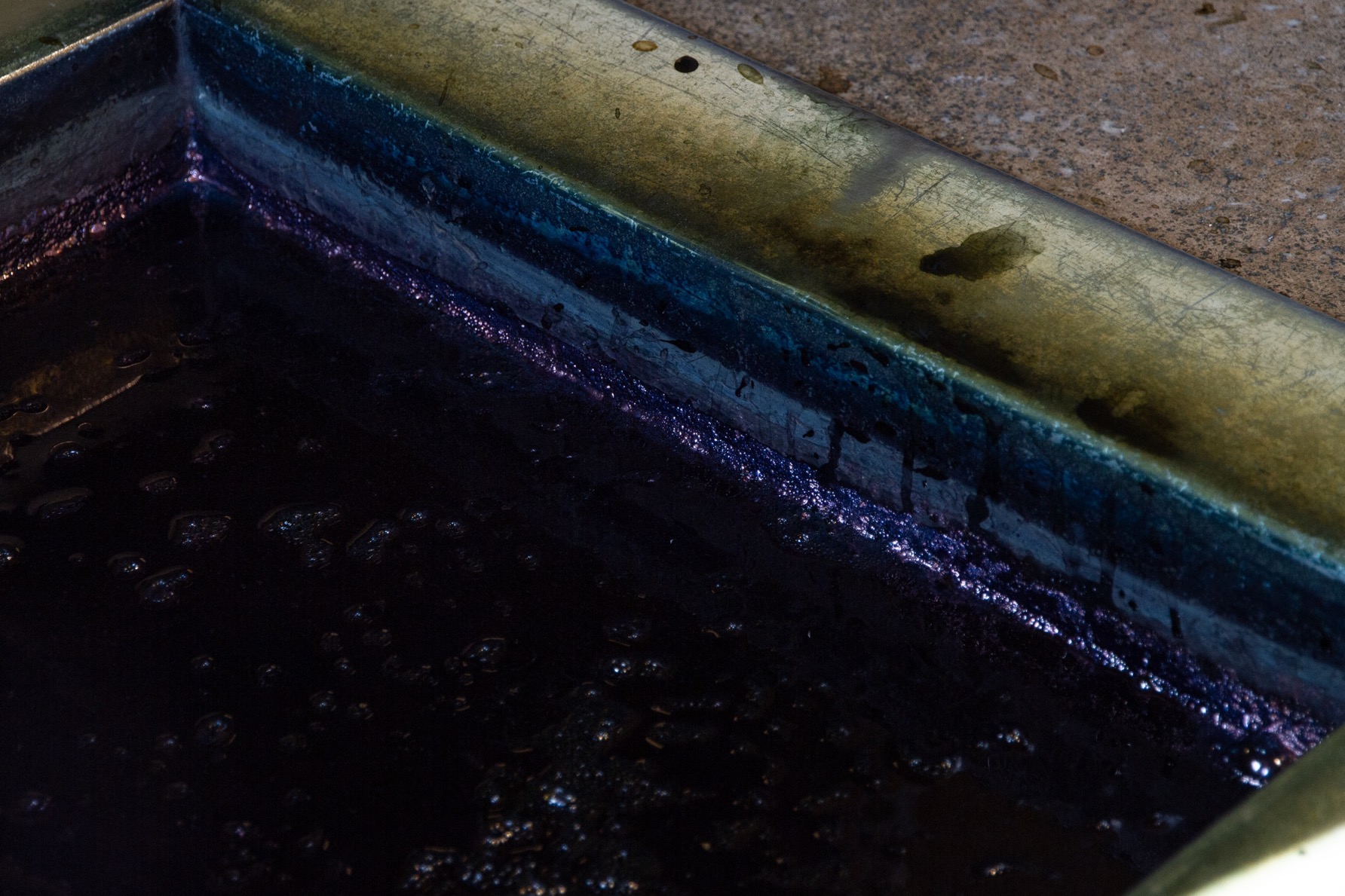
The plant’s leaves are dried and fermented to produce “sukumo,” a botanical dye, which takes about a year of meticulous attention from artisans known as “aishi.” This sukumo is then gradually fermented using a method called the “natural indigo lye fermentation process,” in which lye, sake, bran, and coal are used to gradually increase the volume of the dye. The process of creating the indigo dye liquid, referred to as “ai o tateru,” takes about one week to ten days from the start of fermentation until the indigo is finally ready to be used to dye cloth.
Itajime Dyeing Process
Board assembly and tightening
The process begins with the thorough washing of boards previously soaked in water for storage, ensuring that the fine grooves remain unclogged by the dye. Subsequently, while inspecting the pattern, the boards are assembled, and the fabric is delicately positioned between them, striving for both horizontal and vertical alignment to achieve an exquisite pattern solely through the artisan’s tactile sense. The width of the fabric influences the outcome: finer folds in wider fabric may yield more white areas, while narrower widths tend to result in greater dyed sections. Upon securely sandwiching the fabric between the boards, they are tightly clamped from both sides to secure their position.
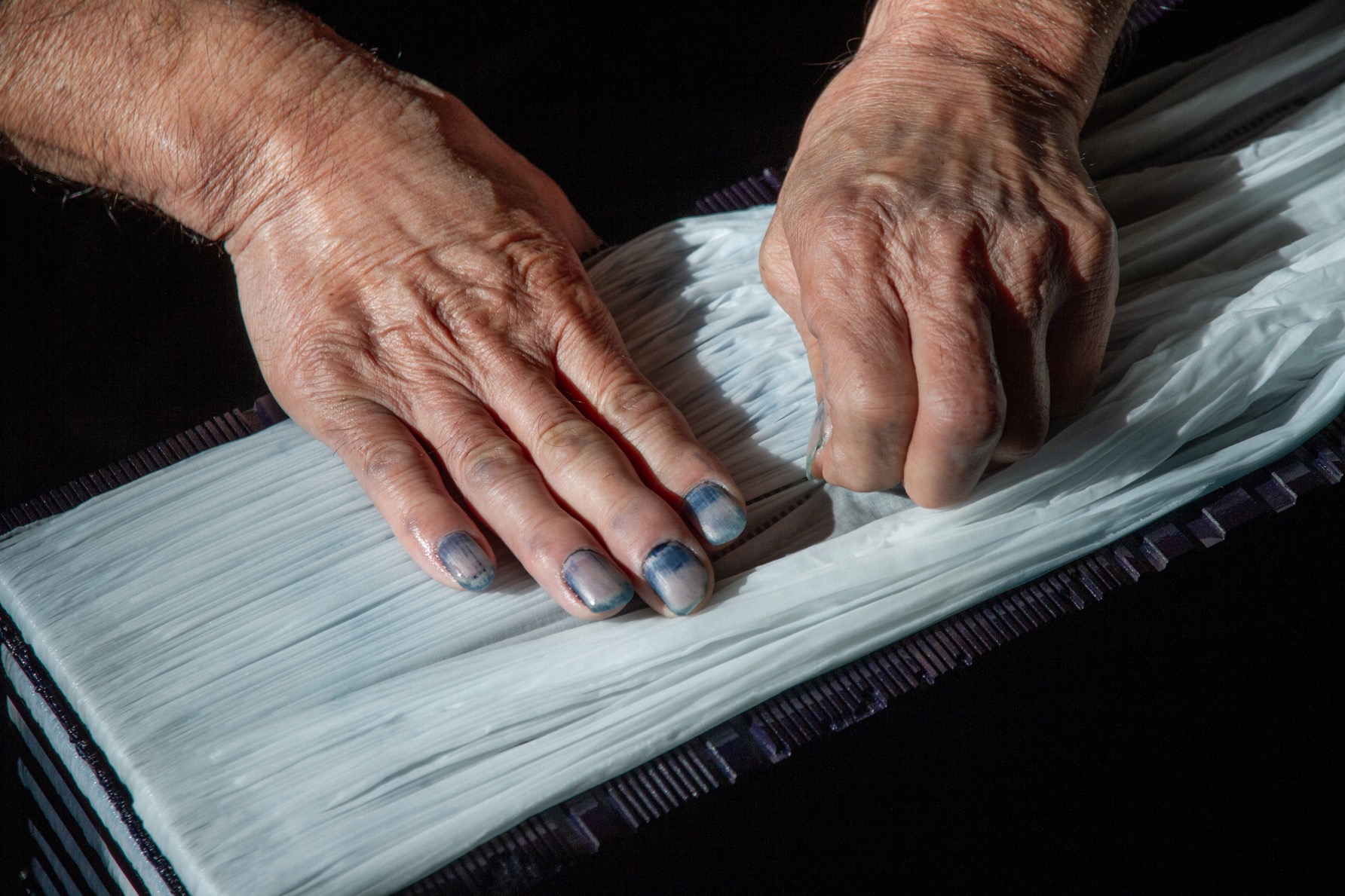
Indigo dyeing, washing, and sun-drying
To bring out the intricate pattern, a newly prepared indigo dye solution is used, and the fabric is immersed in the dye solution at a temperature of 30-32 degrees Celsius, with the boards raised by a machine. During this process, the fabric is lifted and lowered multiple times to agitate the dye solution inside, ensuring it reaches the pattern lines to prevent air pockets. After soaking, the fabric is lifted for oxidation, and the process is repeated while monitoring the indigo’s condition. Adjustments are made, such as switching the top and bottom positions or tilting the boards to accelerate oxidation and ensure the liquid enters fine areas.
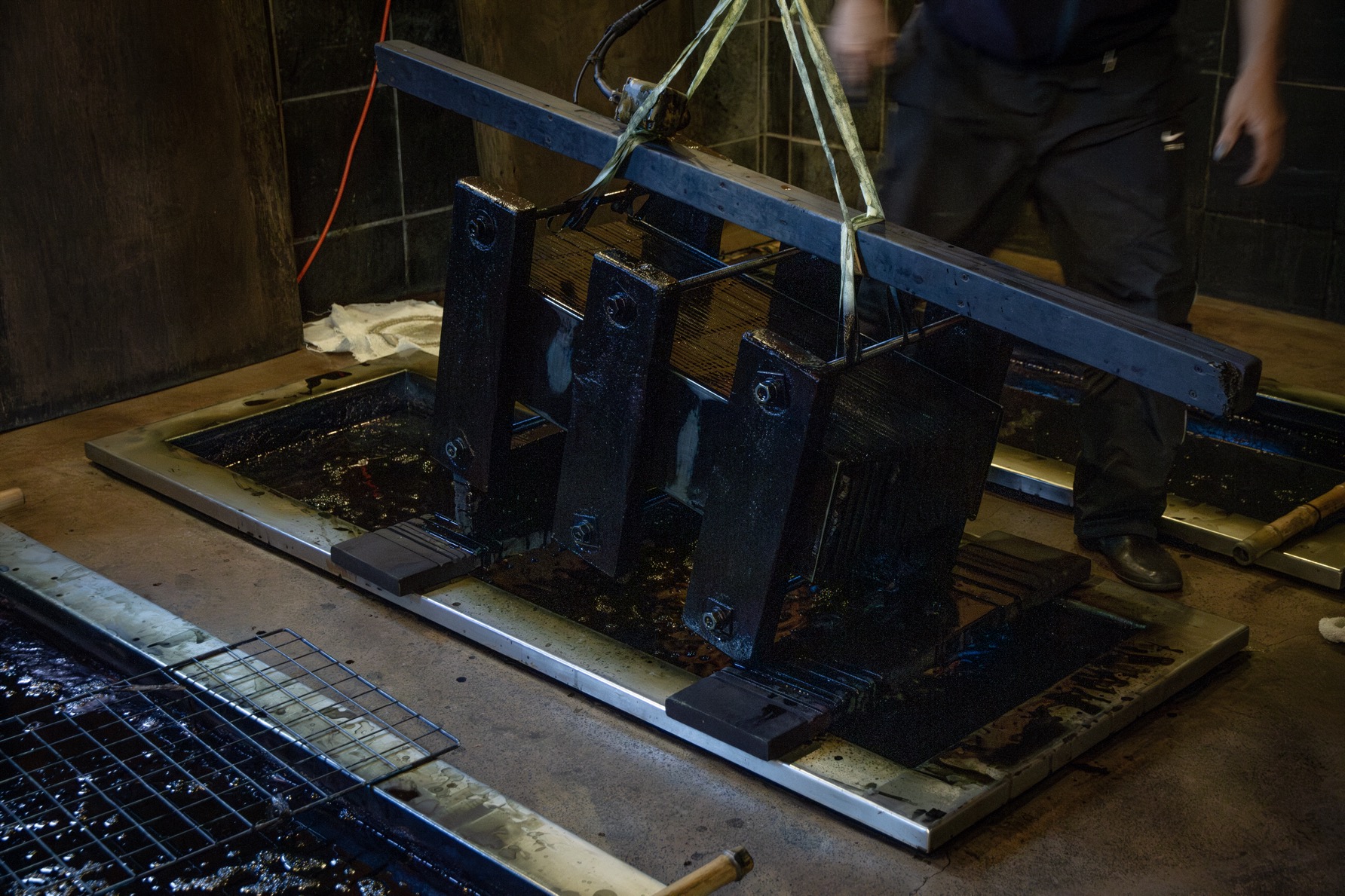
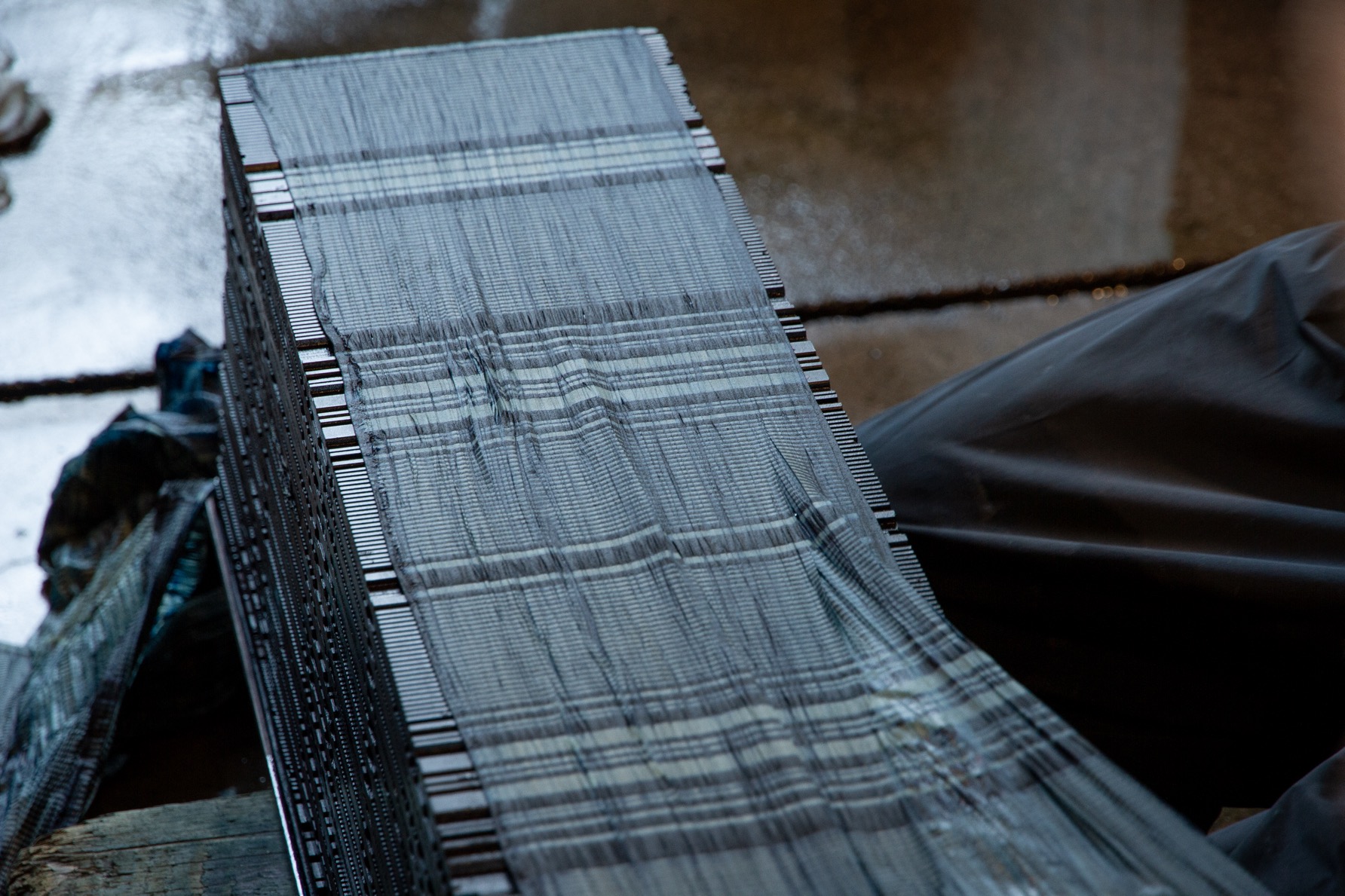
Once the dyeing is complete, the boards are dismantled, and the fabric is removed and hand-washed in a washing area filled with water, spreading the fabric out while washing. After dehydration, the fabric is spread out loosely for sun-drying to avoid strain on the fabric. The next day, it is soaked in lye and subjected to hot water rinsing to facilitate the release of tannins* contained in sukumo, followed by sun-drying again. Sun-drying not only dries the fabric but also exposes it to UV light, helping to lift the yellowish tint caused by tannins. By repeating this washing and sun-drying process for about four days, the yellowish blue transforms to a greenish blue and finally to a vibrant, clear blue, while the white becomes whiter with sharper contours emerging.
*Tannin: A type of polyphenol found in plants, known as a component of astringency.
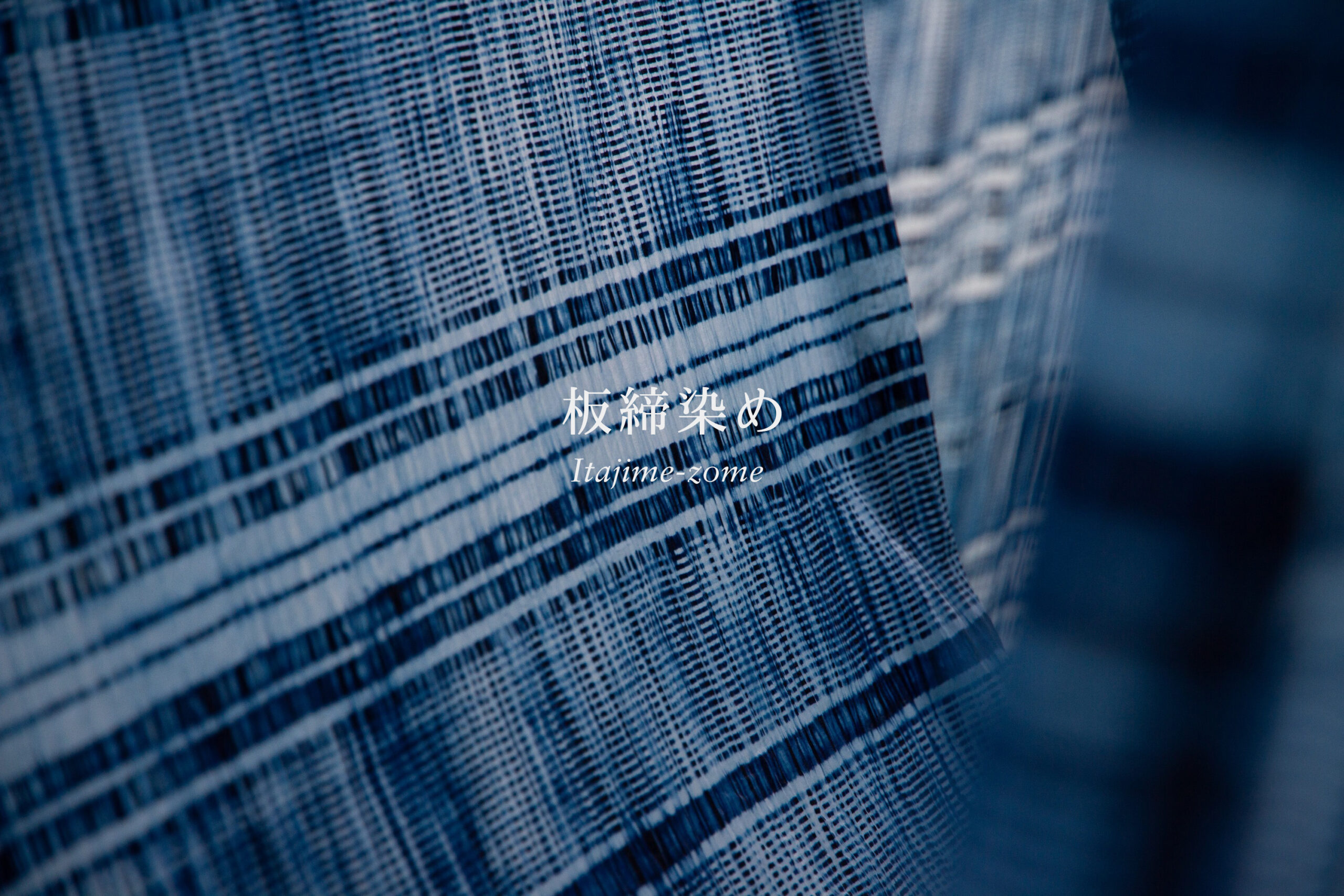
Using the fabric dyed through these meticulous processes of Itajime dyeing, we have crafted comfortably cool and visually refreshing items perfect for early summer. We invite you to see the items firsthand at our stores.
Acknowledgment: Kosoen
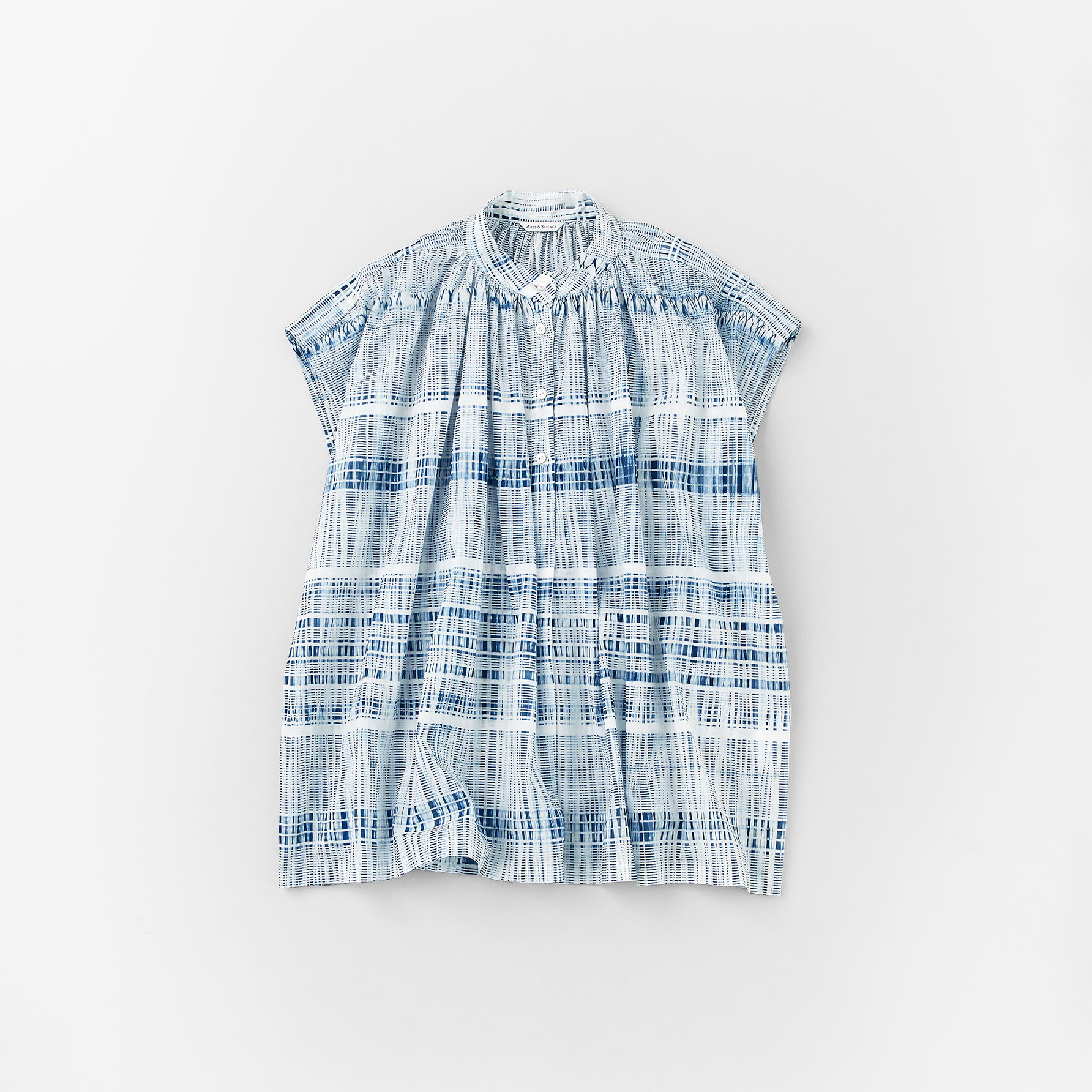
Button Front No Sleeve Gather Blouse
- MATERIAL
100% cotton (ITAJIME Ai check lawn)
- SIZE
1
- COLOR
ITAJIME Ai dark
- PRICE
¥103,400 (¥94,000 excl. tax)
- STORES
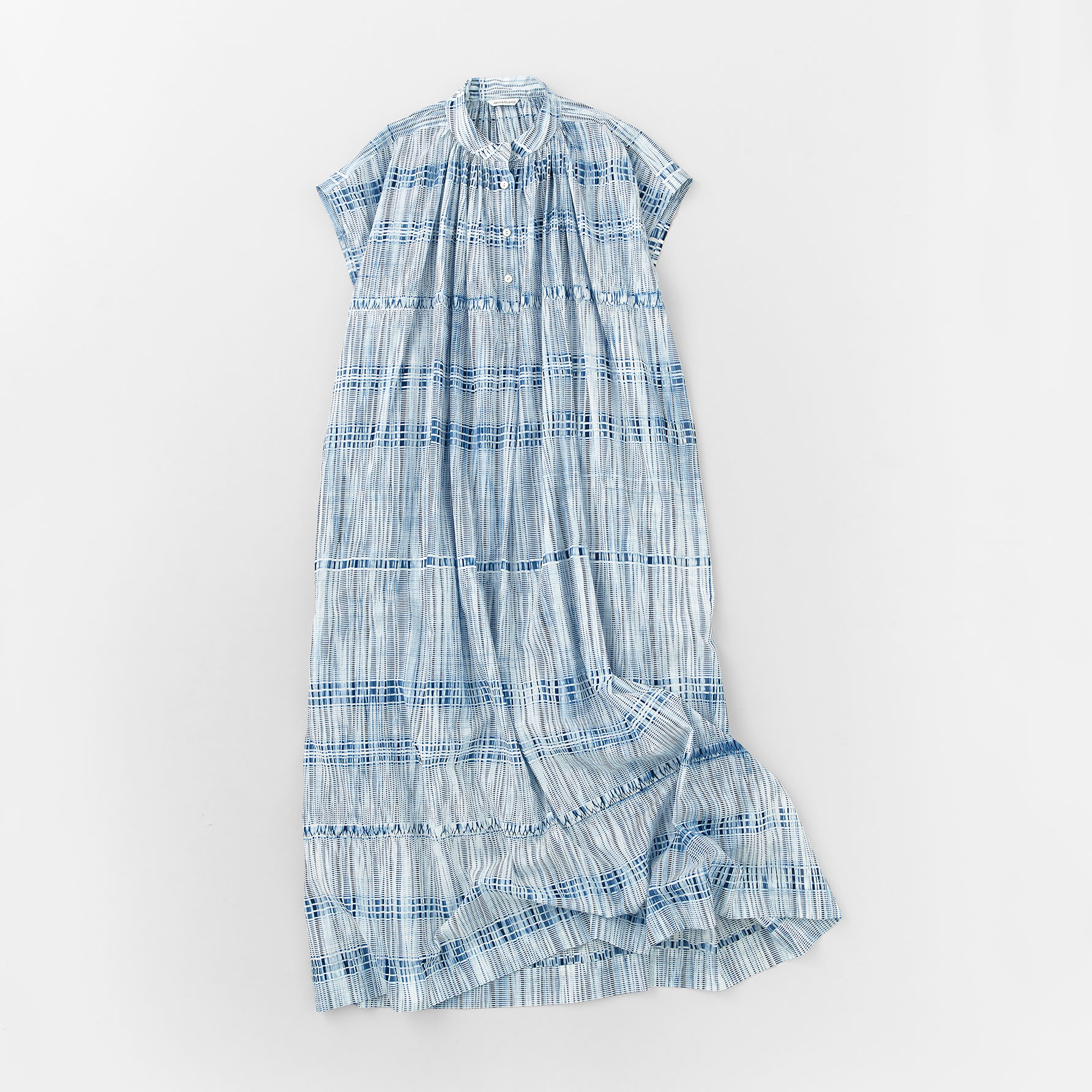
Button Front No Sleeve Gather Dress
- MATERIAL
100% cotton (ITAJIME Ai check lawn)
- SIZE
1
- COLOR
ITAJIME Ai dark
- PRICE
¥176,000 (¥160,000 excl. tax)
- STORES
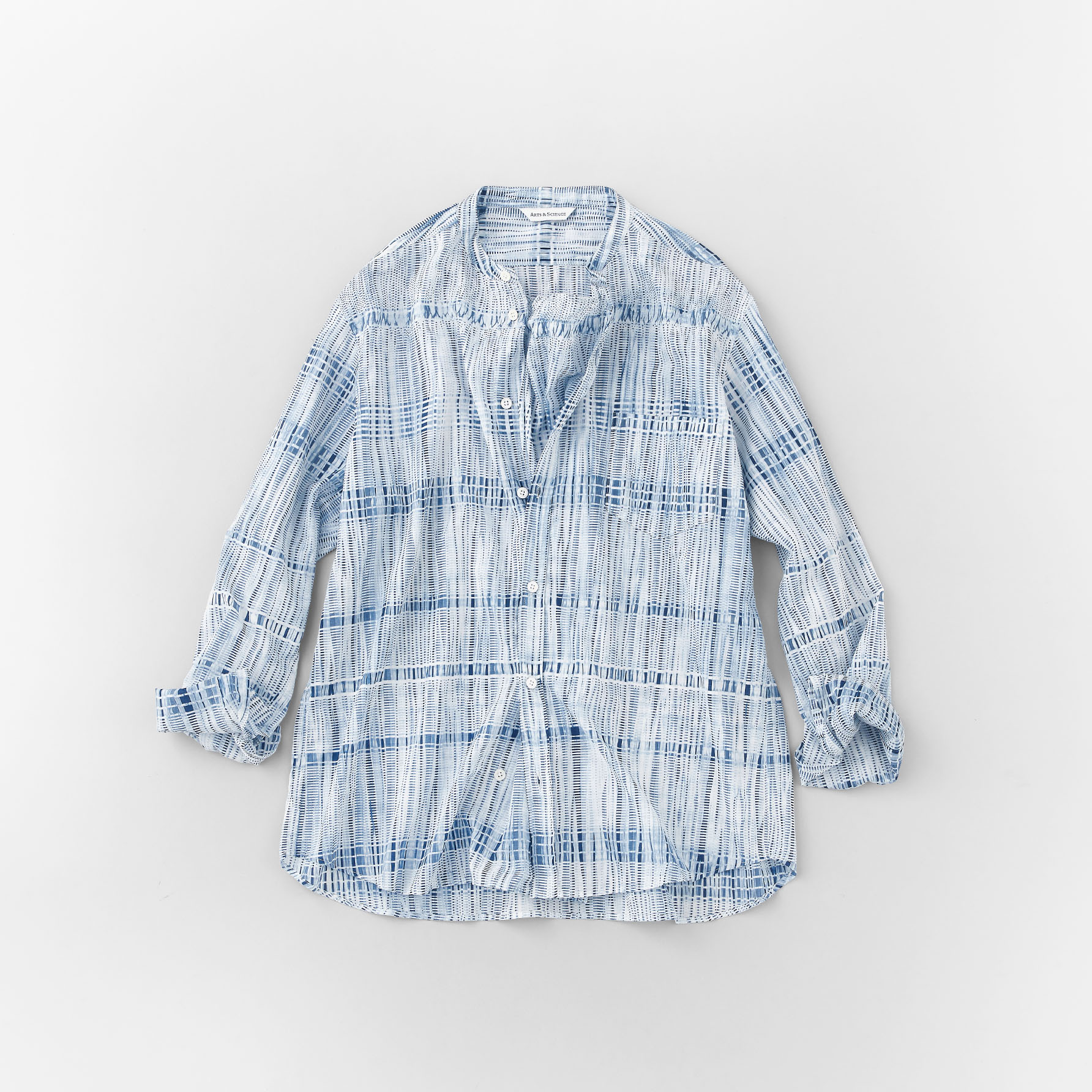
No Collar Fake Shirt
- MATERIAL
100% cotton (ITAJIME Ai check lawn)
- SIZE
1
- COLOR
ITAJIME Ai dark
- PRICE
¥118,800 (¥108,000 excl. tax)
- STORES
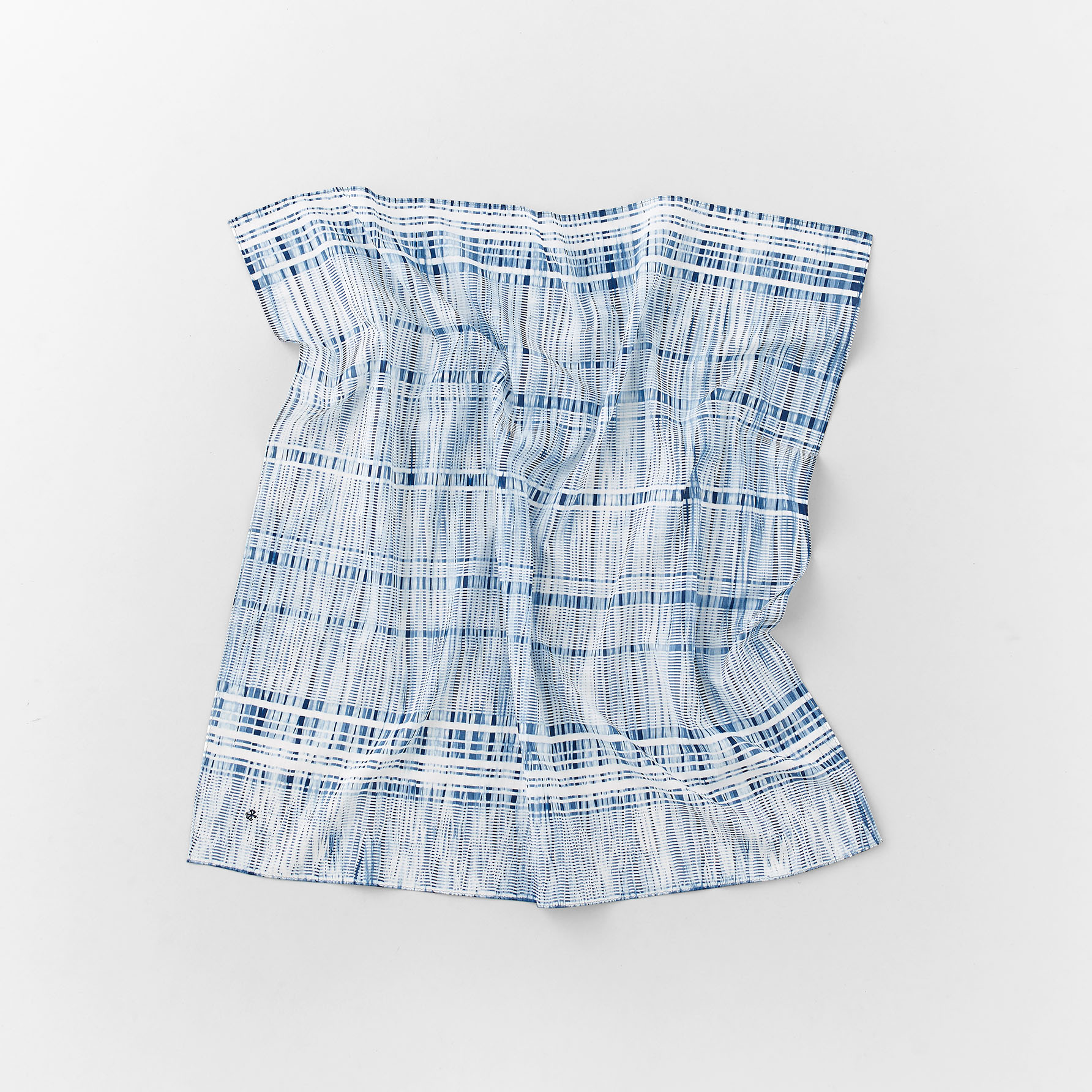
Square Scarf S
- MATERIAL
100% cotton (ITAJIME Ai check lawn)
- SIZE
65cm × 65cm
- COLOR
ITAJIME Ai dark
- PRICE
¥28,600 (¥26,000 excl. tax)
- STORES
For inquiries, please contact each shop directly or use our contact form.